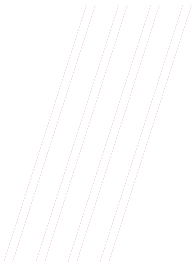
ITW upholds our position of strength by meeting the needs of today and innovating for the future. By engineering cleaner, more efficient end-use solutions, we help our customers achieve their sustainability goals.
Driven By Customer-Back Innovation
We believe that innovations are most impactful when they address the specific needs and concerns of our customers. This concept, which we call Customer-Back Innovation, is a key component of the ITW Business Model and fuels high-quality growth. ITW’s long history of innovation is demonstrated by our broad portfolio of approximately 21,000 granted and pending patents. In 2024 alone, we increased our new patent filings by 18% as we work to protect our customer solutions.
At the core of Customer-Back Innovation is the belief that customers’ needs can change significantly over time. Therefore, in addition to launching new products, we also make serial, long-term improvements that address new imperatives as they emerge. Increasingly, customers are interested in Clean-Tech solutions — products that support environmental efficiency and help customers reduce the impacts of their operations and products. The need for more sustainable solutions is a key growth opportunity for ITW, and we are proud to report nearly one-third of our revenue is from Clean-Tech products. Based on these customer needs, our Clean-Tech solutions have focused on the following:
- Designing products that support more sustainable technologies, such as electric vehicles, wind turbines and building materials
- Serial innovation to continually reduce the energy and resources our products require to operate or manufacture
- Incorporating recycled material or more sustainably sourced material into manufactured products
- Developing technologies to test the durability and sustainability of materials and products to better inform customer decisions and development
ITW’s Clean-Tech Products
In 2024, ITW sold more than $5 billion of Clean-Tech products, representing approximately 32% of ITW’s 2024 revenue.
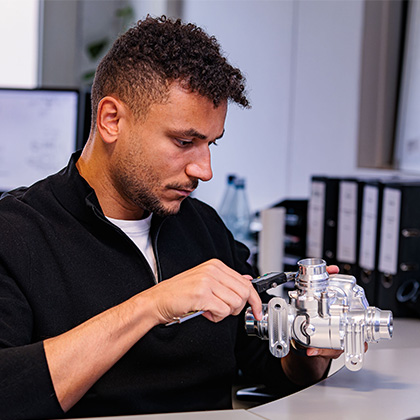